Introduction to Hazardous Locations
Hazardous locations are environments where the presence of flammable gases, vapors, dust, or fibers creates a potential risk of explosion or fire. These areas, often found in industries such as oil and gas, chemical processing, pharmaceuticals, and grain handling, demand strict safety protocols and proper classification to ensure both worker safety and equipment integrity.
- Overview of Hazardous Environments
Industrial settings, especially those dealing with volatile substances, are inherently prone to accidents involving fires or explosions. Even a minor spark from equipment can ignite a catastrophic event if the environment contains the right combination of gases, dust, or fibers. That’s why understanding and accurately classifying hazardous locations is essential to mitigate these risks. - Importance of Proper Classification for Safety
The correct classification of hazardous locations is the foundation for designing and installing electrical equipment that won’t serve as a source of ignition. Without proper classification, the selection of electrical equipment can be ineffective or unsafe, putting lives and production assets at significant risk. The Class/Division system, widely adopted in North America, helps engineers ensure that every piece of equipment is suitable for the specific type of hazard present.
Understanding Explosions in Hazardous Locations
Explosions in hazardous locations occur when three critical elements combine: a flammable substance, an oxidizer (usually air), and an ignition source. The right mix of these components, often referred to as the “fire triangle,” can lead to an uncontrolled combustion reaction—an explosion.
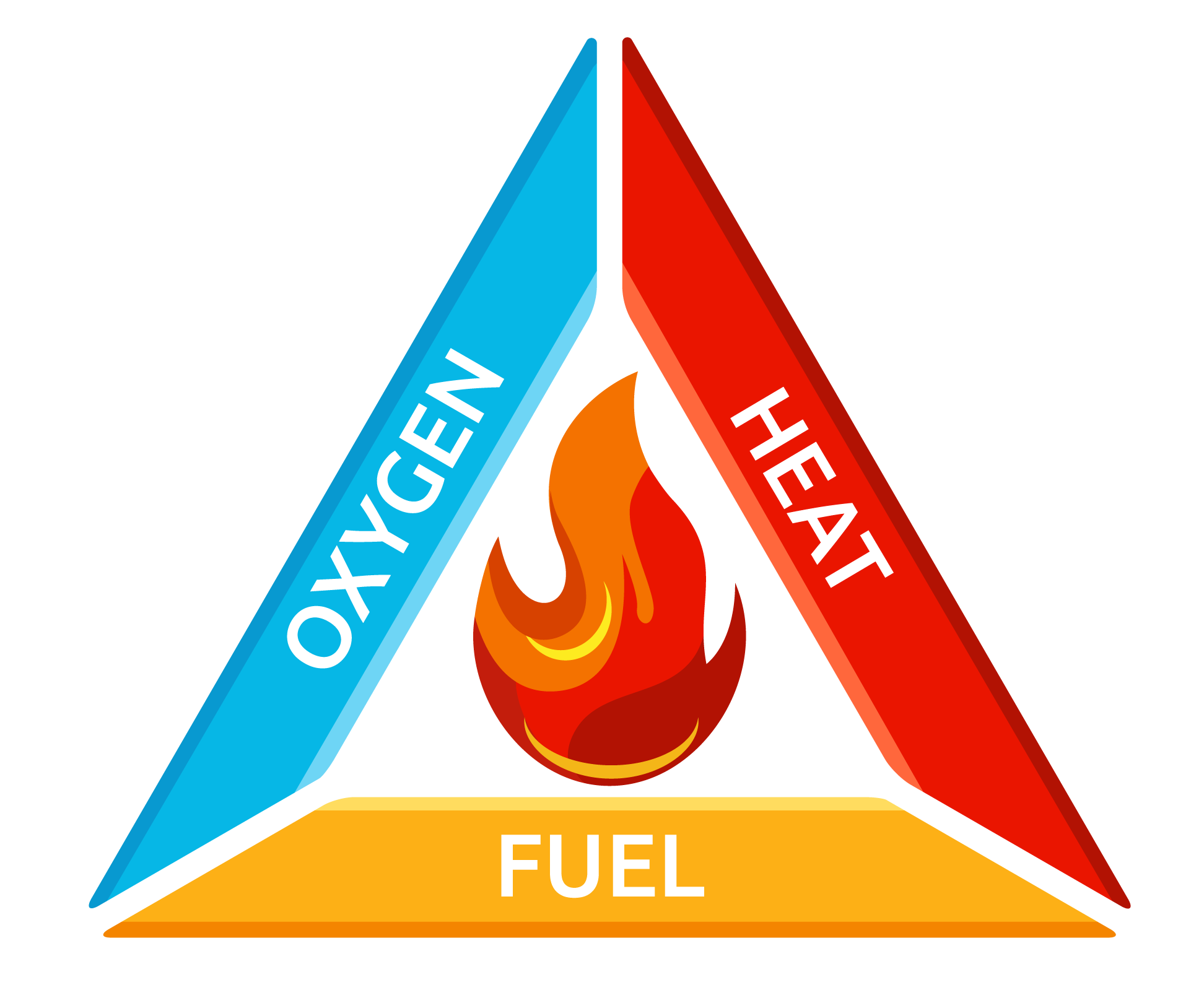
- What is an Explosion?
An explosion is a rapid expansion of gases caused by a sudden release of energy. In hazardous locations, this energy release often occurs due to the ignition of a flammable gas, vapor, or dust cloud. Once ignited, the flammable substance rapidly burns, producing extreme heat, pressure, and shockwaves, which can cause severe damage to equipment and people. The more confined the environment, the greater the risk of significant harm. - When and Why Explosions Occur
Explosions are most likely to happen when flammable substances are present in sufficient quantities and are exposed to a source of ignition. This could be something as simple as an electrical arc from equipment, static electricity, or even heat generated from friction or poorly ventilated motors. In normal industrial processes, managing these risk factors is critical—proper classification helps ensure that the equipment used in hazardous locations doesn’tcontribute to accidental ignition.
Class/Division System Explained
The Class/Division system is the standard in North America (defined by NEC and CEC) for classifying hazardous locations based on the type of flammable materials present and the likelihood of their presence during regular operations. This system divides locations into three classes, which indicate the general type of hazard, and two divisions, which specify the frequency or likelihood of the hazard being present.
- Class Definitions
- Class I: These areas are hazardous due to the presence of flammable gases or vapors, such as in oil refineries, chemical plants, or gas processing facilities. Class I locations are particularly dangerous because gases and vapors can easily ignite and explode when exposed to ignition sources.
- Class II: Locations where combustible dusts are present. These areas include grain elevators, sugar mills, and coal processing plants. Dust particles suspended in the air, in high enough concentrations, can explode if they come into contact with an ignition source.
- Class III: This class covers areas where ignitable fibers or flyings are present. These are typically found in industries like textiles, woodworking, and paper manufacturing. Although fibers and flyings are less likely to cause explosions, they can still pose a fire hazard.
- Division Definitions
- Division 1: This division refers to areas where hazardous materials (gases, vapors, dust, or fibers) are present under normal operating conditions. In Division 1 locations, the risk of an explosion is higher because the hazardous substance is expected to be present consistently during normal operations.
- Division 2: In these areas, hazardous materials are only present under abnormal conditions, such as equipment failure or accidental leaks. The likelihood of an explosion is lower in Division 2, but the potential for danger still exists if a hazardous material is released unexpectedly.
Components Required for an Explosion
For an explosion to occur, three essential components need to be present: a flammable substance, an oxidizer, and an ignition source. These three elements form the well-known “fire triangle,” which, when combined in the right conditions, can result in a potentially catastrophic explosion.
- Flammable Substance
The flammable substance can be a gas, vapor, dust, or fiber, depending on the hazardous environment. For instance, in Class I locations, gases like methane, propane, or hydrogen are common flammable substances. In Class II locations, materials like grain dust, coal dust, or metal dusts pose significant explosion risks. The key is ensuring these substances are controlled or contained, as their presence in the right concentration is a crucial factor in explosion risk. - Oxidizer
The most common oxidizer is the oxygen found in the air, which can readily support combustion when mixed with a flammable substance. In most industrial settings, oxygen is always present, meaning that two of the three elements of the fire triangle—fuel and oxidizer—are almost always readily available. Managing the risk requires eliminating or reducing the presence of the third element: ignition.
Classification of Hazardous Locations
Classifying hazardous locations is essential for ensuring safety in environments where flammable gases, vapors, dust, or fibers are present. These classifications help determine what type of equipment can be used, what safety precautions should be in place, and how to mitigate explosion risks. In North America, this is done using the Class/Division system, which is part of the National Electrical Code (NEC) and Canadian Electrical Code (CEC).
Class I: Gases and Vapors
Class I locations are areas where flammable gases or vapors are present in the air in sufficient quantities to ignite or explode. These areas are commonly found in industries like oil refineries, chemical plants, and gas processing facilities.
- Division 1:
- Flammable gases or vapors are present during normal operations.
- These areas are constantly exposed to the hazardous substances, making them highly dangerous.
- Examples: Areas near valves, pumps, or vessels in chemical plants where gas leaks are part of the process.
- Division 2:
- Flammable gases or vapors are present only under abnormal conditions, such as equipment failures or leaks.
- The hazard is not normally present, making these areas less risky compared to Division 1.
- Examples: Storage tanks or pipelines where leaks might occur under emergency conditions.
Class II: Combustible Dust
Class II locations involve the presence of combustible dust, which can ignite and explode when suspended in the air. These areas are found in industries such as grain processing, woodworking, and coal handling.
- Division 1:
- Combustible dust is present during normal operations in sufficient quantities to cause an explosion.
- The dust may be in suspension or accumulate on surfaces where it can later become airborne.
- Examples: Grain elevators, coal processing plants, and areas around dust producing machinery.
- Division 2:
- Combustible dust is not normally present in the air, but it can accumulate on surfaces under abnormal conditions.
- These areas are less likely to have combustible dust in the air, but a fire or explosion can still occur if the dust becomes suspended.
- Examples: Warehouses or areas adjacent to dust-producing operations where dust may accumulate.
Class III: Fibers and Flyings
Class III locations involve areas where ignitable fibers or flyings (larger, flammable particles) are present. These fibers generally do not create an explosive atmosphere but can still pose a significant fire risk.
- Division 1:
- Easily ignitable fibers or flyings are present during normal operations.
- These areas have constant exposure to the hazard, making them prone to fire.
- Examples: Textile mills, paper mills, and plants that handle wood or plastic fibers.
- Division 2:
- Ignitable fibers or flyings are not present during normal operations but may accumulate under abnormal conditions.
- Examples: Storage or handling areas for materials that produce fibers or flyings, where there is a low likelihood of them being present.
Detailed Class/Division Example Scenarios
Class I, Division 1 Example
In an oil refinery, certain areas are classified as Class I, Division 1, such as around valve seals or tank venting systems. Here, gases like propane, methane, or hydrogen are continuously present due to process leaks or emissions during normal operations. Electrical equipment in these zones must be explosion-proof, ensuring that any internal sparks or arcs are contained and do not ignite the surrounding flammable atmosphere.
Class I, Division 2 Example
In a natural gas compressor station, pipelines transport gas at high pressure, and while gas is not continuously present in the air, there is a risk of leaks during abnormal conditions. These compressor stations may develop minor leaks at connections, flanges, or valves, especially during maintenance activities, or if a pipeline experiences pressure fluctuations.
Under normal operating conditions, the area around these pipelines would not contain flammable gas in quantities high enough to create an explosive atmosphere, as the system is designed to prevent leaks. However, should a leak occur due to equipment failure or maintenance errors, flammable gas could briefly enter the area.
Thus, the area surrounding the pipelines and compressors is classified as Class I, Division 2:
- Hazardous Atmosphere: Gas is only present in abnormal conditions (e.g., equipment failure, leaks).
- Equipment Requirements: Electrical and electronic devices must be designed to avoid ignition sources if gas enters the area, ensuring the equipment remains safe under potential leak conditions.
- Safety Measures: Regular leak detection systems, robust maintenance practices, and gas alarms further minimize risk.
Class II, Division 2 Example
In a flour mill, the grinding process produces combustible dust. However, a nearby packaging area, where dust isn’t normally suspended in the air, would be classified as Class II, Division 2. Though dust may accumulate on surfaces over time, it only becomes hazardous if disturbed, such as during maintenance. Electrical equipment in these areas must prevent dust from entering enclosures to avoid accumulation and overheating, which could ignite the dust.
Key Safety Considerations for Each Classification
- Class I Locations: Equipment must be designed to contain any sparks, arcs, or heat that could ignite the surrounding gases or vapors. This includes explosion-proof enclosures, intrinsically safe systems, and gas tight seals.
- Class II Locations: Dust-tight enclosures are critical to prevent dust from entering equipment where it could accumulate and overheat. Equipment may also need to be surface temperature-rated to ensure that it does not ignite dust layers.
- Class III Locations: While fibers and flyings don’t typically form explosive atmospheres, equipment must still be designed to prevent sparks or overheating that could ignite flammable materials. This often includes careful management of equipment cooling and ensuring that materials don’t accumulate near heat-generating parts.
Designing Explosion-Proof Electrical Equipment
To prevent electrical equipment from becoming a source of ignition, explosion-proof designs and specific construction methods are employed. These designs must meet regulatory standards set by the National Electrical Code (NEC) or the Canadian Electrical Code (CEC) to ensure safety in hazardous locations.
1. Non-Sparking Components and Intrinsic Safety
- Non-Sparking Materials: Electrical devices and components should be made from materials that minimize friction and sparking risks. Non sparking materials, especially for mechanical connections, can reduce the chance of ignition if gas unexpectedly enters the area.
- Intrinsic Safety for Low-Energy Devices: For control circuits, sensors, and low-power equipment, intrinsic safety is a key approach. By limiting energy levels within the circuits, intrinsic safety design ensures that any potential sparks or heat do not reach ignition levels. This approach is common in instruments like pressure sensors and flow meters.
2. Sealed Enclosures and Conduit Protection
- Explosion-Proof Enclosures: While Class I, Division 2 equipment does not require the same level of enclosure as Division 1, enclosures must still prevent hazardous gases from entering and reaching internal components. Materials should be sturdy enough to contain any accidental internal sparks.
- Seal-Off Fittings: Conduits and electrical connections must include seal off fittings to prevent gas migration from hazardous areas into non-hazardous zones. Conduit seals are particularly important where equipment extends from a Class I, Division 2 area into a safe zone.
3. Temperature Control and Rating Compliance
- Surface Temperature Ratings: Devices must be rated with a surface temperature low enough to avoid igniting gases present under abnormal conditions. Equipment like motors, lighting, and heaters must meet temperature limits set by NEC or IEC standards.
- Thermal Management Designs: Equipment should incorporate design features to manage excess heat—such as heat sinks, fans, or specialized enclosures—to ensure surface temperatures remain well below the ignition threshold, even under heavy loads.
4. Voltage, Current Limiting, and Arc Prevention
- Control and Power Circuit Limits: Voltage and current are carefully managed in Class I, Division 2 equipment to lower the risk of arcs. For instance, using low-energy circuits in control systems minimizes risk. For higher-power devices like motors, explosion-proof controls, or relay systems located in safe zones, are ideal to reduce ignition hazards.
- Use of Sealed or Encapsulated Relays: Relays and motor starters are often either encapsulated or sealed to avoid arcing, especially during switching actions. Where feasible, these components can be installed in non-hazardous zones, further minimizing ignition risks.
5. Regular Maintenance and Gas Detection Monitoring
- Routine Inspections: Regular maintenance and inspections are essential to ensure that enclosures, seals, and conduit fittings are intact and performing as designed. This is critical for preventing gas from leaking into electrical compartments and potential ignition sources.
- Gas Detection and Alarming: Some Class I, Division 2 areas benefit from gas detection systems that monitor for leaks or unexpected releases. In the event of gas detection, alarms alert personnel to evacuate or shut down equipment to prevent ignition in abnormal conditions.
Methods of Explosion Protection in Hazardous Locations
Explosion protection in hazardous locations is about eliminating the risk of ignition. There are several methods employed to achieve this, each designed to either prevent the explosive atmosphere from coming into contact with an ignition source or to contain an explosion if one occurs. These methods are crucial in industries where the presence of flammable materials is a constant threat.
- Confine the Explosion
One of the most common methods is to design equipment that can contain an explosion within itself. This is done using explosion-proof enclosures that prevent internal explosions from spreading outside the equipment. The enclosure must be strong enough to withstand the internal pressure caused by the explosion without rupturing or transmitting the flames to the surrounding atmosphere. Explosion-proof motors, lighting fixtures, and junction boxes often use this method, particularly in Class I, Division 1 areas. - Limit the Energy
Another technique is to limit the energy available within the system to a level that cannot ignite an explosive atmosphere, even if a fault occurs. This is typically achieved through intrinsically safe systems. In such designs, all electrical and electronic circuits are designed to operate on low power, ensuring that even if a short circuit or other fault occurs, the energy released is too low to cause ignition. Intrinsically safe equipment is particularly useful in environments like oil refineries, where the risk of gas leaks makes the use of traditional high-energy systems dangerous.
Summary of Protection Methods
Summarizing the key explosion protection strategies helps emphasize the importance of selecting the right methods for different hazardous locations. Each method is designed to address a specific aspect of the risk and can be used in combination to provide comprehensive protection.
Key Strategies for Mitigating Explosion Risks in Hazardous Areas
The primary methods include:
- Explosion Containment: Using enclosures to keep any potential explosion within the equipment.
- Intrinsic Safety: Ensuring the energy within the equipment is too low to ignite any surrounding flammable substances.
- Segregation/Isolation: Physically separating the hazardous substances from the potential ignition sources using barriers or other isolating techniques. These strategies, when applied according to the correct classification (Class, Division, and Group), help ensure the safety of both personnel and equipment in high-risk environments.
Marking and Labeling of Explosion-Proof Equipment
Proper marking and labeling of explosion-proof equipment are critical for ensuring compliance and safety in hazardous locations. Markings provide detailed information about the equipment’s suitability for specific hazardous conditions, ensuring that it is installed and used correctly.
- NEC/CEC Marking Requirements
The National Electrical Code (NEC) and the Canadian Electrical Code (CEC) require explosion-proof equipment to be marked with specific information, including the Class, Division, Group, and temperature rating. These markings help engineers and technicians quickly determine if the equipment is appropriate for the hazardous location in which it will be used. For instance, equipment marked as “Class I, Division 1, Group C” indicates it is suitable for areas with flammable gases and vapors that may be present during normal operation. - Temperature Rating
Temperature classification is an essential part of equipment labeling. The maximum surface temperature that equipment can reach must be lower than the ignition temperature of the hazardous material present. This ensures that the equipment does not become a source of ignition due to heat buildup, even under fault conditions. Proper temperature ratings are critical for preventing explosions in environments with combustible dust or flammable gases.
Comparing the Class/Division System with the Zone System
In addition to the Class/Division system used in North America, many parts of the world use the Zone system for classifying hazardous locations. Both systems aim to ensure safety but differ in how they categorize hazardous areas.
- Class/Division vs. Zone System
The Class/Division system (used primarily in North America) categorizes hazardous locations based on the presence of hazardous substances and their frequency (Classes I, II, III, and Divisions 1 and 2). In contrast, the Zone system (used internationally and in Europe) classifies hazardous locations into zones based on the probability of the presence of flammable substances.- Zone 0: Hazardous substances are present continuously or for long periods.
- Zone 1: Hazardous substances are likely to be present during normal operations.
- Zone 2: Hazardous substances are unlikely to be present and, if they are, it is only for a short duration.
- Advantages and Challenges
The Zone system allows for a more granular classification of hazardous areas, which can provide more flexibility in equipment selection. However, it may also require more detailed risk assessments compared to the more straightforward Class/Division system. Both systems have their merits, and in some cases, a hybrid approach can be used when working in global projects.
Execution to NEC/CEC Standards
The National Electrical Code (NEC) and Canadian Electrical Code (CEC) provide stringent guidelines for designing and installing electrical systems in hazardous locations. These standards are essential to ensure that all equipment used in hazardous environments meets specific safety criteria.
- Compliance with NEC/CEC Standards
Equipment installed in hazardous areas must meet NEC or CEC standards, depending on the region. These standards define the proper methods for installing wiring, conduits, and electrical devices in hazardous locations. Following these codes ensures that the installation minimizes the risk of ignition by separating or sealing off hazardous substances from electrical components. - Installation Best Practices
Best practices for NEC/CEC installations include using explosion-proof junction boxes, intrinsically safe barriers, and appropriate sealing techniques to prevent the entry of flammable gases into enclosures. Proper grounding and bonding of electrical systems are also critical to avoiding static discharge in hazardous locations.
Comparing IEC, NEC, and CEC Standards
The IEC (International Electrotechnical Commission), NEC (National Electrical Code), and CEC (Canadian Electrical Code) provide different guidelines for hazardous locations, each with its own approach to classification and equipment requirements. Understanding the differences between these standards is crucial for multinational projects and operations.
- IEC Zones vs. NEC/CEC Classes/Divisions
The IEC uses the Zone system (Zone 0, 1, 2) for hazardous areas, while the NEC/CEC uses the Class/Division system. The key difference is in the frequency and likelihood of hazardous substances being present, with the Zone system offering more detailed differentiation. This distinction is important when sourcing equipment or managing projects that cross international borders, as equipment that complies with one standard may not necessarily meet the requirements of another. - Global Compliance and Certification
Multinational companies often need to ensure that their equipment is compliant with both IEC and NEC/CEC standards. Equipment may require multiple certifications, such as ATEX for Europe (based on IEC standards) and UL or CSA certifications for North America (based on NEC/ CEC standards). Ensuring global compliance is critical for avoiding accidents and maintaining operational continuity in hazardous locations across different regions.