Introduction to Wire & Cable Management
Industrial control panels comprise of control circuits, power circuits, or a combination of both. These circuits generate signals that control the performance of the equipment or machinery connected to them. Wires and cables are integral to these circuits and play a significant role in their functioning. Trends such as maximum efficiency, minimal downtimes, quick turnaround, and time-to-market capabilities are critical to industrial users. These demands are fulfilled using various technological components that are interconnected by a vast network of wires and cables. This increased use of wires and cables stresses on the utilization of an efficient wire and cable management system. This is because wires and cables may clutter the workspace, cause accidents, and inflict several potential issues if they are not managed properly. Before we get into specific products, let's discuss the benefits of wire & cable management.
Benefits of Wire & Cable Management
Effective wire & cable management offers several benefits, including the following:
- Improves Availability: An employee or an operator of a particular industrial control panel, power, communication, or IT rack may get confused seeing a mess of cables and wires. This may lead to human errors, which is one of the main reasons for the downtime of systems. Thus, effective management of wires and cables will help users and operators identify them easily, as well as minimize human errors.
- Improves Performance of Systems: Many times, control and power wires in an industrial control panel and data cables in data centers give rise to issues such as interference and crosstalk, which will further lead to erratic data transfer and potentially severe losses. An efficient wire and cable management strategy helps in differentiating these data and power cables to avoid the risk of interference.
- Improves Safety: Unorganized or tangled cables and wires may cause short circuits and sometimes fire, thereby endangering the lives of people nearby. Proper cable management is key to ensure safety.
- Improves Troubleshooting: Cabling that is unorganized and tangled may lead to stress in a workplace. In case of emergencies, as operators cannot easily identify and service the affected cables, there will be expensive downtimes. An effective cable management solution helps operators quickly identify and access cables in order to troubleshoot the network and hardware appropriately before commencing repair and maintenance.
Best Practices for Wire & Cable Management
The following wire & cable management best practices will help achieve a neat and organized workplace:
- Understand signal classes which are as follows:
- Class 1: This class covers main power lines, as well as power-regulation control devices, switch-mode converters, and power circuits with a high di/dt. This class may interfere with Classes 2, 3, and 4. Class 1 signals are not highly sensitive.
- Class 2: This class covers relay contacts, and may interfere with Classes 1, 3, and 4. Class 2 signals are not highly sensitive.
- Class 3: This class covers digital circuits and may be affected by pulses and surges. It may also interfere with Class 4 signals.
- Class 4: This class is for analog input/output circuits. It is highly sensitive to pulses and surges.
- Physically separate the cables based on the signal class.
- Separate Classes 1 and 2 from the sensitive Classes 3 and 4.
- Ensure that the cable only carries the signals in a single group.
- Over shield the sensitive and disturbing cables to protect them from high frequencies.
- Use separate connectors for different groups.
- Bond the free conductors at the end.
- Avoid using cheap quality cables because they may fail and lead to signal loss.
- Use quality terminations to crimp cables, otherwise, they may require regular maintenance.
- Always use the highest quality metal trunking because it helps improve Electro Magnetic Compatibility (EMC).
- Color code the cables properly to avoid confusion.
- Label every cable according to their signal classes using any of the following:
- Wrap around labels
- Cable flags
- Cable tags
Along with the above-mentioned practices, it is important to use the right kind of wire & cable management. There are several choices when it comes to wire & cable management, among them, wiring and cable ducts and terminal blocks are the most popular and common. Let's take a closer look at these panel essentials.
Wire/Cable Duct Defined
Wire/cable ducts are the wire management solutions that support concealing and routing the wires and cables inside the electrical enclosures, such as control panels. Wiring ducts are mainly designed as rigid cable trays, and they comprise of several features that help organize and route wires and cables inside the enclosure.
Types of Wire/Cable Duct
Wire/cable ducts are mainly available in the following configurations:
- Slotted Wiring Ducts: These wiring ducts feature fingers or slots that enable easy breaking or customization. Wiring ducts are typically available in various sizes and standard colors—white, grey, black, and blue. These wiring and cable ducts are suited for applications where cables and wires are regularly accessed. The slotted wiring ducts are further characterized into the following types based on slot size.
- Narrow Slot: Featuring narrow slots, these wiring ducts are perfect for wires with small diameters. The narrow slots allow wires to easily enter and leave the duct.
- Wide Slot: As the name indicates, these wiring ducts have wide slots, which assures flexibility, as different wire sizes can be easily accommodated within. Also, these wiring ducts provide excellent cable support when compared to narrow slot wiring ducts. The wide slot wiring ducts deliver an organized feel to communication and electrical control panel applications.
- Solid Wall Wiring Ducts: These wiring ducts have no open slots or fingers and are best suited for applications where cables are not frequently accessed.
Standards for Wire/Cable Duct
The manufacturing of wiring and cable ducts is governed by several standards because they carry power wires. An improper production method may lead to disastrous results in the form of broken wires and failure in the long run.
The installation and use of wiring ducts is governed by various standards, which ensure the proper and safe installation of low-voltage wiring. Following are the applicable installation standards and codes regarding the installation of wiring ducts:
- NFPA 70-2017 National Electric Code
- CSA C22.1 – Canadian Electrical Code – Part 1 Safety Standard for Electrical Installations
- IEC 60364 – Low voltage electrical installations
Product design standards applicable to wiring duct include:
- UL 1565
- CSA C22.2 No. 18.5-02
- IEC 61084-2-1
Terminal Blocks Defined
Terminal blocks are insulated, modular connectors that are designed to connect different circuits together. These components are also referred to as terminal connectors or connection terminals. Terminal blocks generally appear as a long strip made up of several individual terminals, hence the name. These conducting terminals and a clamping component form the basis of the terminal block structure. The terminals serve different functions – they can be used to ground the wires, or connect outlets or electric switches to the mains, in the presence of the electrical power. In short, terminal blocks help organize the wires and secure them effectively.
Terminal blocks are found on a variety of power management and industrial devices including motor protection relays, variable frequency drives, power supplies and connectors, programmable logic controllers, traffic controls, and so on.
Types of Terminal Blocks
Terminal blocks are differentiated based on their device type, as well as structure.
- Device Types
- Fuse Holder Terminals: As the name suggests, these terminals include fuses. In case of a short circuit, only the wiring section associated with the fuse holder is affected.
- Ground Circuit Terminals: These are used to ground systems, as well as components. These terminals have a strong resemblance to single level feed through terminals. However, the only difference is the metal connection and the blocks carrying the terminated wire are grounded. Ground circuit terminals are alternative replacements of standard terminal blocks and can be easily integrated into the terminal block rail.
- I/O Blocks and Sensor Blocks: A sensor block is designed to connect different sensor devices, including proximity sensors. I/O blocks are designed to connect a controller and a device.
- Thermocouple Terminal Blocks: These terminal blocks connect different thermocouple leads together. There are two types of thermocouple terminal blocks – one type that has metal connection strip and wire made of the same metal, and another type, where the thermocouple leads are clamped on both sides of the block. In the second type, the metal connection strip within the block is not utilized.
- Power Distribution Blocks: Blocks mainly used for electrical power distribution. These terminal blocks allow power distribution from a single input to multiple outputs.
- Disconnect Terminal Blocks: In these blocks, wires can be easily disconnected by lifting knife switch or a lever. Disconnect terminal blocks are also known as switch blocks, because they allow easy connection and disconnection without affecting the wiring.
- Structure Types
- Single Level Pass-Through Terminal Blocks: These blocks have a single input terminal and single output terminal. Owing to their basic design, these blocks are mainly used to connect two wires. These terminal blocks are also referred to as single-feed terminal blocks.
- Dual Level Terminal Blocks: These terminal blocks feature two connection terminals in a space-saving arrangement. The second connection terminal is stacked above the first one.
- Three Level Terminal Blocks: These terminal blocks feature three connection terminals in a stacked arrangement. In addition to space saving, this arrangement enables multiple connections in a single block.
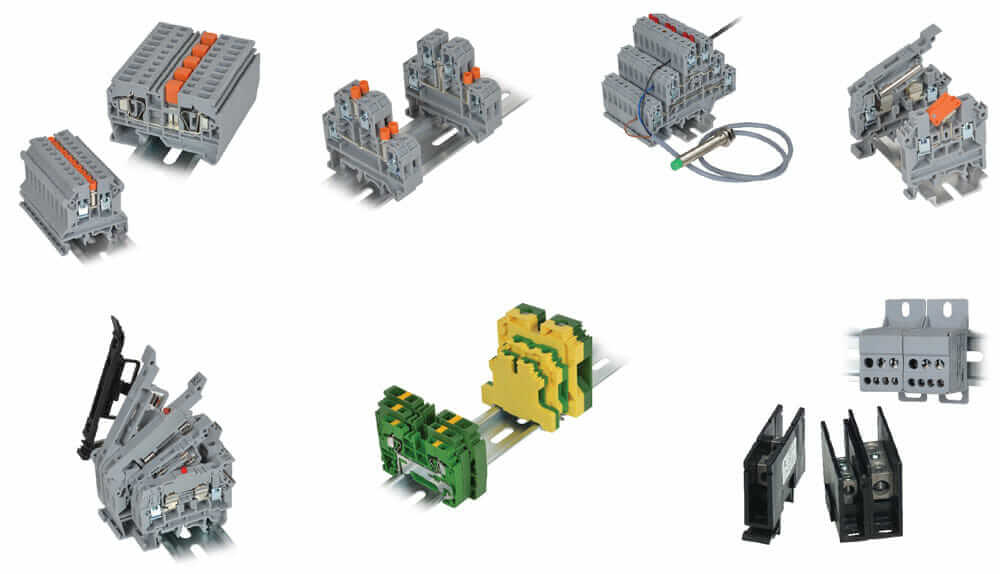
Important Terminal Block Specifications
Terminal blocks differ in their design and purpose; hence it is important to consider their specifications during selection. The most important specifications include:
- Mounting: Terminal blocks are mounted in one of three ways:
- Snapped on the DIN Rail: The DIN rail used for this purpose is made of metal. Terminal blocks are normally mounted on DIN rails such as top-hat rails, miniature top-hat rails, and G32 rails.
- Mounted on the Printed Circuit Board (PCB): The terminal blocks mounted on the printed circuit boards are sometimes referred to as electronic blocks. These terminal blocks feature integrated pins for mounting. Sometimes they are plugged into the pinstripe on the printed circuit board.
- Fixed with Screws on the panel.
- Termination Options: The wire connection in the termination blocks is achieved in one of the following ways:
- Screw Clamps: This is one of the basic termination options, where the wire is tightened on the conductor strip in the terminal block with a screw. The screw terminals are designed to support a wide range of conductors and wire sizes.
- Spring Clamps: In this type of termination, the wire clamping is retained utilizing the pressure of a spring. Mostly used for small wires, these clamps are becoming fast replacements for screw clamps.
- Insulation Displacement Connectors (IDC): In this type of termination, the wire is inserted between the sharp pieces of metal to make a connection.
- Tab Connections: These connections are designed for easy insertion or removal, and thus not soldered. Tab connections are most commonly referred to as blade or spade terminals.
- Push-in Terminal Blocks: In these blocks, the wire is connected by a simple insertion. These terminations use a ferrule, which helps strengthen the ends of a conductor or wire. There are push-in terminal connections that allow direct insertion of a strained conductor or a solid conductor. The conductor is further fixed using a screwdriver.
- Barrier Terminal Blocks: Designed for applications where vibration can be an issue, these terminal blocks feature a ring terminal or a spade that is attached to a wire and inserted through a bolt. This bolt is tightened using a nut on the terminal block. This helps prevent wire loosening during vibrations.
- Contact Specifications: The term contact indicates a wire that is connected to the block. It is also known by names such as poles, ways, or positions. Hence, the number of contacts and corresponding wires are important considerations to be made while buying a terminal block.
- Wire Specifications: Owing to their modular construction, terminal blocks can easily accommodate a wide range of conductor sizes or wires. In North America, the wire size is expressed in units of American Wire Gauge (AWG). The current carrying capacity of the wire depends on its cross-sectional area. The higher gauge numbers indicate small wire diameters. For instance, the AWG 22 wire will have a smaller wire diameter than the AWG 12 wire.
- Orientation: Terminal blocks are mainly available in three different orientations: 45°, 90°, and 180°.
Common Terms Associated with Terminal Blocks
The following terms are common to terminal blocks:
Poles: This term is used to indicate the number of adjacent terminals or individual circuits in the terminal block.
Pitch: It is the distance between two adjacent poles. It is measured in different ways. However, during the measurement, the similar features are considered. The pitch is also known as the center-to-center distance.
Current Rating: This is the maximum current per pole of the terminal block. The current rating is a combination of several factors, including conductivity of the terminal, the cross-sectional area, the power dissipated, and the heat rise at particular rated current.
Voltage Rating: It is the maximum voltage recommended for a terminal block. The voltage rating is again a combination of factors such as the dielectric strength of the housing and the pitch. Voltage rating is also based on the minimum spacing between the conductors, as well as the dielectric withstand. The dielectric withstand is also known as the withstand voltage.
Torque Rating: As with any other electrical circuit, this is the maximum torque that the hardware used can withstand when the wire is being fastened.
Wire Range: This is the maximum and minimum wire sizes that can be accommodated in a terminal block.
Things to Consider While Selecting Terminal Blocks
The selection of terminal blocks will mainly depend on the specifications. However, there are various other things that need to be considered while selecting the right terminal block. They are:
- Consider the factors such as voltage, current, and wire size required for individual wire runs of a particular power distribution application.
- Consider the space requirements of the application.
- Determine the total number of blocks or poles required for the appropriate functioning of the application. Some blocks may require jumper connections, and in such cases, it is important to identify the total number of jumper connections to be performed. These connections can be performed in many ways, such as jumper comb, connector/side, top-cross, etc.
- Choose from the special function block such as disconnect, ground, fuse, switch, indicating types, etc.
- Analyze where the isolation partition is to be made in the terminal block. These separations will help contain creepage in the terminal assembly, as well as create better visual separation.
Applicable Terminal Block Standards and Compliance
Terminal blocks are designed in accordance with the following standards:
- National Electrical Manufacturers Association (NEMA): Terminal blocks are designed for heavy duty applications. Featuring binder head screws, self-lifting pressure plates, and box lug connectors, these terminal blocks offer excellent options for several high current applications. NEMA terminal blocks, also known as American-style blocks, allow easy wiring owing to their open construction.
- International Electrotechnical Commission (IEC): These are basically DIN blocks, which allows maximum terminations in per linear foot. Although these blocks have originated in Europe, they are recognized worldwide. DIN terminal blocks are valued for their compact designs, and offer excellent design flexibility. These blocks can be interchanged between different manufacturers because DIN rails are manufactured in standard sizes only.
Compliances
Terminal blocks are designed to comply with the following standards:
- UL 1059
- CSA 22.2 No. 158
- IEC 60947-1 and 60947-7-1
c3controls Terminal Block Offerings
From standard feed-through spring clamp or screw clamp to disconnect, fuse holder, and power distribution terminal blocks, we’ve got a solution to simplify your wiring and enhance you panel quality while saving on valuable installation time:
- IEC Terminal Blocks available in both screw clamp and spring clamp connections from 5mm to 25mm with ratings from 20A to 232A. Accepts wires as small as 0.5mm2 (24 AWG) and as large as 120mm2 (4/0 AWG). A variety of color-coded blocks for easy circuit identification. Accessories available.
- High Density Terminal Blocks available in multiple terminal points from 4, 6, and 12 in a single molded housing. Rated 30A @ 600V AC and 30A @ 750V AC continuous service. Accommodates #18 to #10 AWG (0.34 – 4mm2) stranded or solid copper wire. Available panel mounting or 35mm DIN rail mounting for easy assembly. Accessories available.
c3controls Wire Duct Offerings
Series WD Wiring Duct from c3controls will speed your wire/cable management and installation. The wide variety of types and options will increase productivity, reduce installation costs, and will give you the most attractive and organized control panels in the industry!
c3controls offers rigid, ‘U’ shaped wire duct with a non-slip cover available in grey and white. There are 13 selectable dimensions from 25mm wide up to 80mm, and up to 2 meters in length. Optional adhesive backing.
Check out our wire duct offerings!
Panel Solutions
For your complete panel needs, c3controls operates a UL508A certified panel shop serving the OEM and panel builders across a wide variety of industries. Check out our enclosed panel solutions!
c3controls Panel Essentials Papers: